What are the steps to use the vacuum homogenizing emulsifier?
What are the steps of using the emulsifier?
What are the steps to use the vacuum homogenizing emulsifier?
1. Usually connect the cooling water of the mechanical seal before turning on the vacuum homogenizing emulsifier, and shut down the cooling water when shutting down. Tap water can be used as the cooling water. The cooling water pressure is less than or equal to 0.2Mpa. The material must enter the working cavity to start the machine, and it is necessary to ensure that it does not run under the condition of material interruption to avoid idling, which will cause the mechanical seal (mechanical seal) to burn out due to high temperature or affect the service life. The cooling water inlet and outlet joints are equipped with hoses with 5mm inner diameter.
2. After the emulsifier confirms that the machine-sealed cooling water is turned on, start the motor, and repeatedly require that the rotation of the motor should be consistent with the rotation mark of the spindle before it can operate. Reverse rotation is strictly prohibited!
3. When using the dispersing emulsifying homogenizer, the liquid material must be continuously input or kept in a certain amount in the container. Empty machine operation should be avoided to avoid damage to the equipment due to high temperature or crystal solidification of the material during work, idling is strictly prohibited!
4. Generally, it is only necessary to enter the material into the TRL1 pipeline equipment through the high self-weight, and the feed must be continuously input to keep the material with good fluidity. When the fluidity of the material is poor, when the viscosity is ≧4000CP, the inlet of the SRH pipeline equipment should be equipped with a transfer pump, and the pumping pressure is 0.3Mpa. The choice of pump should be a colloid pump (cam rotor pump) or the like, whose flow matches the flow range of the selected pipeline emulsifier. (Should be greater than the minimum flow value, less than the maximum flow value)
5. It is strictly forbidden for metal shavings or hard and difficult-to-break debris to enter the working cavity to avoid devastating damage to the working stator, rotor and equipment.
6. Once the nanoemulsifier has abnormal sound or other faults during operation, it should be shut down immediately for inspection, and then run again after the fault is eliminated. Clean the working chamber, stator and rotor after shutdown.
7. If the process chamber can be equipped with an additional insulation layer for cooling or heating the material, the coolant or heat transfer oil should be connected first when the machine is turned on. The working pressure of the insulation interlayer is ≤0.2Mpa. When processing temperature requirements (such as asphalt), it must be heated or cooled to normal working temperature, cranked, and turned on.
8. When the colloidal emulsifier is used in a flammable and explosive working environment, an explosion-proof motor of the corresponding level must be selected.
9. After the production is completed, the equipment must be cleaned up, so as to maintain the working efficiency of the stator and rotor and also protect the sealing of the machine. When necessary, a set of cleaning circulation device is designed and installed near the periphery.
10. According to the different media used by the user, the import and export filters must be cleaned regularly to avoid reducing the feed volume and affecting the production efficiency. The materials entering the working cavity must be fluid, and materials with dry powder and agglomerates are not allowed to enter the machine directly, otherwise, it will cause the machine to become stuffy and damage the equipment.
11. The stator and rotor of the three-stage pipeline type emulsifier need to be checked regularly. If excessive wear is found, the corresponding parts should be replaced in time to ensure the effect of dispersion and emulsification.
12. If liquid leakage is found at the shaft during operation, the pressure of the mechanical seal must be adjusted after shutdown. (Attached at the back: detailed introduction when using mechanical seal).
13. Before using this equipment, work out corresponding safety production operating procedures to ensure the safety of operators and equipment. The user of the electrical control system should set up a safety protection system and have a good and reliable electrical motor grounding device.
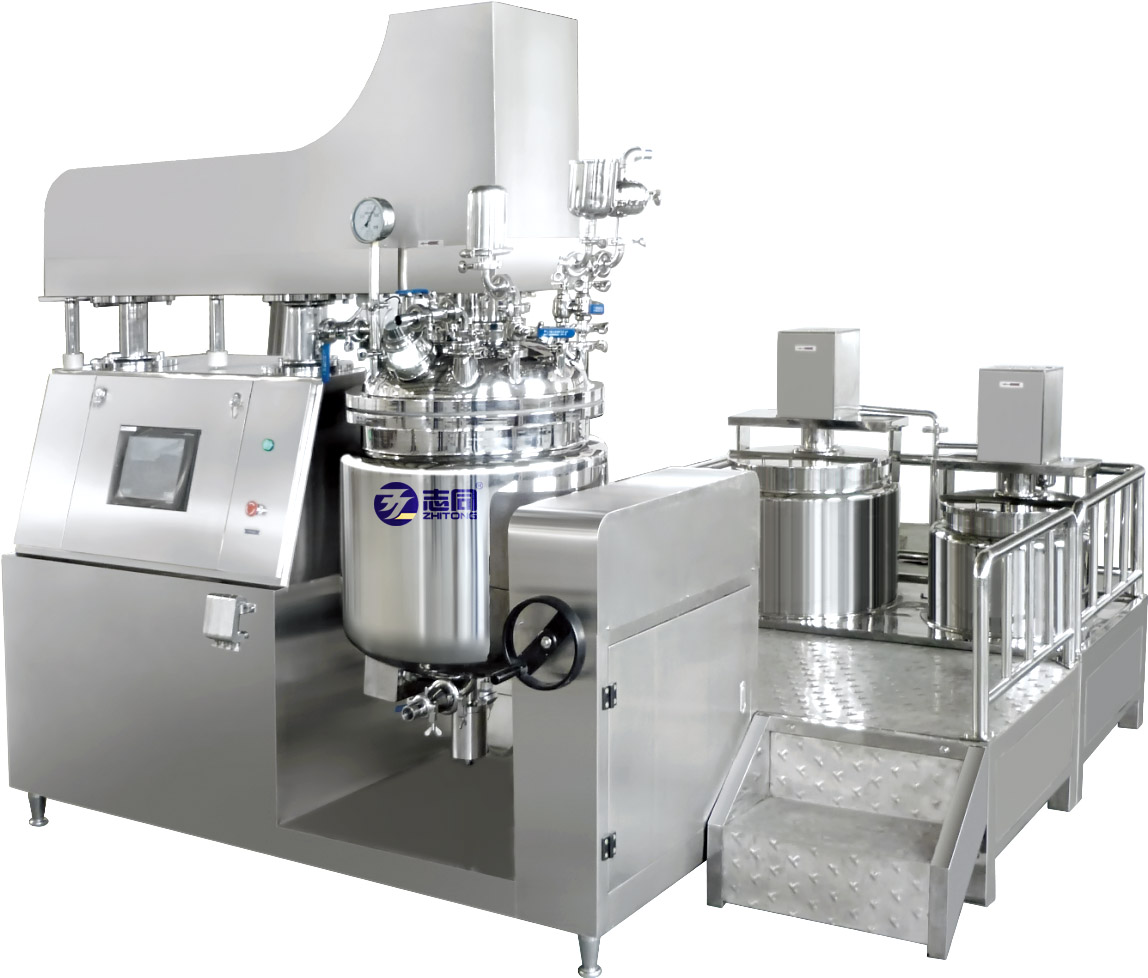
Post time: Oct-10-2021